Khám phá nhà máy sản xuất Lexus LFA - Kỳ 2: Các phương pháp xử lý CFRP
Từ việc không có bất kỳ kinh nghiệm nào về kỹ thuật xử lý và chế tạo các chi tiết carbon gia cường CFRP, Toyota sau 10 năm nghiên cứu triển khai dự án Lexus LFA nay đã sở hữu trong tay một bí quyết công nghệ ưu việt mà trên thế giới không nhiều hãng có được.
Nguyên lý sản xuất cơ bản của Carbon Fiber Reinforced Polymer (CFRP) thật ra không mới. Thậm chí trước cả kim loại. CFRP là một dạng composite, làm từ hai loại vật liệu khác nhau, đan xen vào nhau thành một loại vật liệu mới bền chắc hơn. Rơm rạ nhào trộn với đất sét là một dạng composite, hay hiện đại hơn như bê tông cũng được xem là composite. Trong trường hợp CFRP thì các sợi carbon được kết hợp với nhựa epoxy. Đôi lúc người ta có thể gọi CFRP là vật liệu nhựa được gia cường bằng sợi carbon (carbon fiber reinforced plastic), tuy nhiên, sản phẩm cuối cùng có đặc tính khác xa so với nhựa thông thường mà đa số đều biết đến.
CFRP có tỷ số độ cứng và độ bền trên khối lượng vượt trội. Tuy nhiên CFRP cũng đồng nghĩa với chi phí sản xuất đắt đỏ. Loại vật liệu này chỉ được dùng để sản xuất xe đua, nơi mà tiền bạc không phải là vấn đề. Bước vào phòng sạch mà Toyota dùng để sản xuất các chi tiết bằng CFRP cho LFA, lý do tại sao mẫu xe thể thao này có giá bán cao ngất hiện ra rõ ràng.
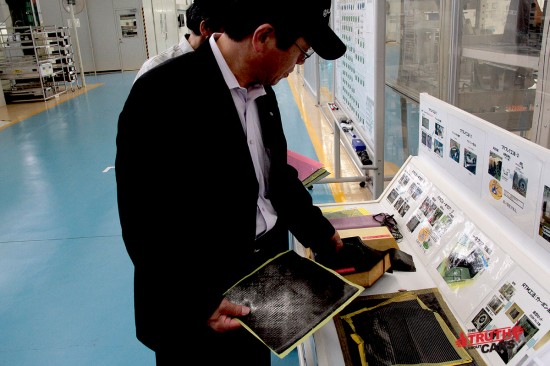
Tanahashi giới thiệu các tấm carbon Pre-preg.
Về cơ bản, có ba cách khác nhau để tạo nên vật liệu CFRP: Pre-preg, Resin Transfer Molding (RTM) và Sheet Molding Compound (SMC), lần lượt theo thứ tự giảm dần của độ bền cũng như chi phí sản xuất. Lexus LFA sử dụng cả ba phương pháp này, tùy thuộc vào đặc tính cần có của chi tiết.
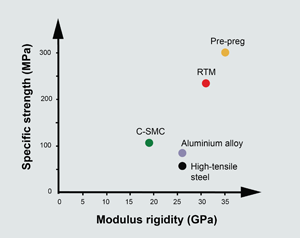
Độ cứng và khả năng chịu lực của các loại carbon theo 3 phương pháp sản xuất khác nhau so với thép và hợp kim nhôm.
Các chi tiết có độ bền và cứng cao nhất trên LFA được sản xuất bên trong phòng sạch. Bất cứ ai bước vào căn phòng này đều phải trùm tóc lại, mang đồ bảo hộ kín mít và được hút sạch bụi từ trên xuống dưới.
Phòng sạch không chỉ không có bụi bẩn mà nhiệt độ phòng cũng luôn được duy trì ở mức 22 độ C và độ ẩm ổn định thường xuyên 60%. Bước qua cánh cửa chắn khí để vào căn phòng là khu vực xử lý Pre-preg. Đây là phương pháp tạo ra các chi tiết có độ bền cao nhất nhưng cũng đắt nhất.
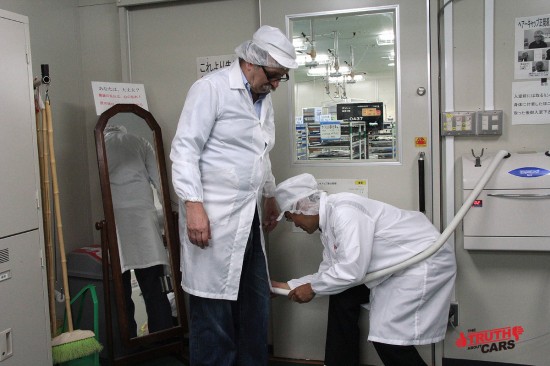
Tẩy “uế” trước khi vào phòng sạch.
Tất cả các tấm sợi carbon thấm nền nhựa mua từ các nhà cung cấp đều được cất giữ trong phòng lạnh trước khi đem ra sử dụng. Mỗi tấm đơn như vậy bao gồm hai lớp sợi, thớ sợi carbon trong mỗi lớp được đặt theo các hướng chéo nhau để tăng độ bền.
Tại khu vực xử lý, các tấm này được máy hút dính định vị trên chiếc bàn lớn. Một đầu bút điều khiển bằng máy tính sẽ viết lên bề mặt tấm các mã số linh kiện. Sau đó, đầu bút được tự động thay thế bằng một mũi cắt. Trong vòng 20 phút, tấm carbon bị chia ra thành từng mảnh ghép rời.
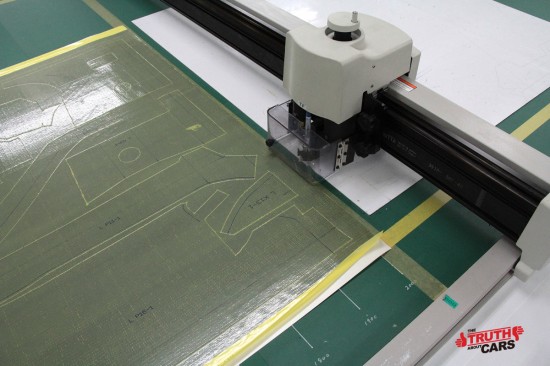
Mũi cắt chia tấm carbon Pre-preg thành nhiều mảnh rời.
Cách đó không xa, một nhóm công nhân đang thực hiện các công đoạn trong qui trình sản xuất phần khung của bảng điều khiển dưới sự giám sát chặt chẽ của một đốc công.
Với đôi găng tay trắng, các công nhân này sắp xếp 335 tấm carbon rời lên một chiếc khuôn. Thỉnh thoảng họ sử dụng một thiết bị như máy sấy tóc để uốn nắn những tấm carbon này theo hình dạng mong muốn, và để tránh bụi len lõi giữa các lớp.
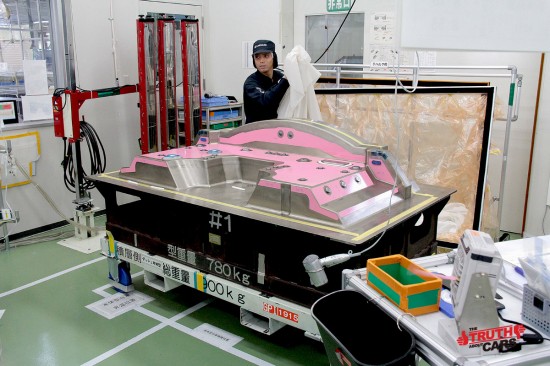
Khung bảng điều khiển bắt đầu quá trình hình thành của mình từ bộ khuôn này.
Giống như một chiếc bánh cưới khổng lồ, 13 lớp carbon Pre-preg được lắp ghép cẩn thận thành một chi tiết mà sau đó sẽ là khung của bảng điều khiển. Mỗi lớp được liên kết với nhau bằng màng urê trộn nhôm và cố định bằng các đinh tán.
Mỗi bộ khung bảng điều khiển bao gồm 335 mảnh carbon rời này đều được đánh dấu trong bảng hoàn công. Bảng hoàn công phải có chữ ký của quản đốc, và sau đó được ký thêm một lần nữa bởi người kiểm soát chất lượng.
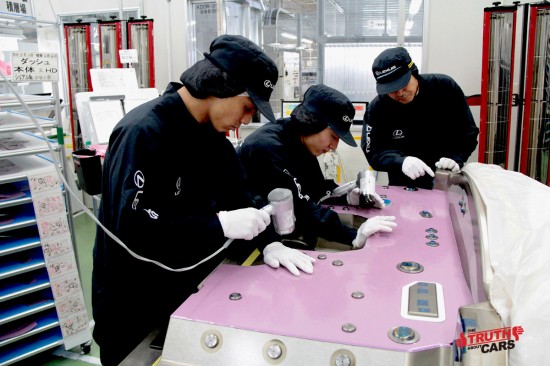
335 mảnh carbon rời được ghép thành một khối thống nhất.
Mất 8 tiếng để ghép một bộ khung như vậy bằng tay. Và khi hoàn thành, chi tiết này được bọc kín trong một màng chân không đặc biệt, rồi đem ủ. Việc bọc kín và rút chân không khiến chi tiết ép sát vào khuôn. Quá trình ủ diễn ra trong nồi hấp khổng lồ bên cạnh phòng sạch, có áp suất 2 bar (gấp đôi áp suất khí quyển) và nhiệt độ duy trì ổn định 65 độ C, thời gian ủ lại kéo dài 8 tiếng nữa, cho đến khi chi tiết đạt đến trạng thái liên kết hoàn hảo.
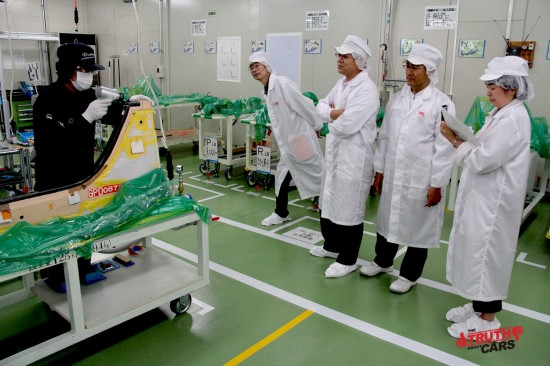
Một người làm việc, 4 người giám sát.
Nồi hấp được sử dụng gần như không ngừng nghỉ, đây là điểm dừng chân duy nhất trong quá trình chế tạo các chi tiết cho LFA lại kéo dài tới 2 ca làm việc. Suốt cả ngày, khung bảng điều khiển và một số các chi tiết khác được “nướng” bên trong ống áp suất này, đến đêm, công đoạn “nướng” mới hoàn thành. Đây là lý do khiến tốc độ sản xuất Lexus LFA chỉ đạt một xe mỗi ngày, khả năng thu lợi từ dự án bị giới hạn khiến người ta dễ dàng xóa sổ nó. Nếu so sánh, trong thời gian một bảng điều khiển CFRP được sản xuất, các loại máy thông thường có thể “phun” ra 1.000 bảng điều khiển bằng nhựa, có độ cứng kém hơn nhiều, nặng hơn và chi phí rẻ hơn nhiều. Sự hoàn hảo bao giờ cũng có cái giá của nó!
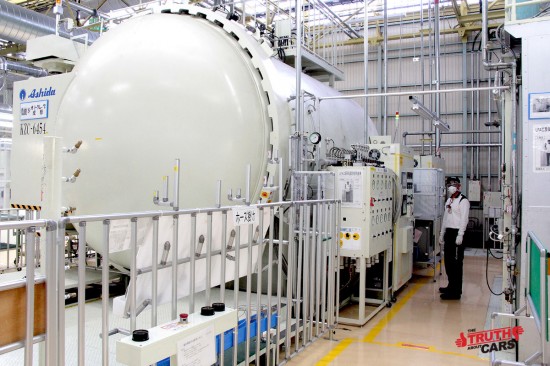
Nồi hấp, nơi mà các chi tiết carbon của LFA ngừng di chuyển trong cả 2 ca làm việc.
Rối rắm như cửi dệt
Cởi bỏ bộ đồ bảo hộ trắng, khách tham quan được đeo một chiếc mặt nạ. Nhưng lần này là để bảo vệ chính họ. Hít phải bụi carbon siêu nhỏ có thể gây tổn hại đến sức khỏe, mà ở khu vực tiếp theo, khách tham quan sẽ tiếp cận một cỗ máy kỳ lạ, thường phát tán các hạt bụi như vậy. Nếu từng tìm hiểu lịch sử của Toyota, nhìn thấy cỗ máy này người ta có thể liên tưởng ngay đến chiếc máy dệt mà Toyota đã phát minh vào năm 1906, nay đã trở thành một di sản của họ (xuất phát điểm của Toyota là một công ty dệt). Nhưng thay vì dệt vải, máy “dệt” hiện đại này đang tết những sợi carbon, và rất có thể sẽ là một phần quan trọng trong tương lai của Toyota.
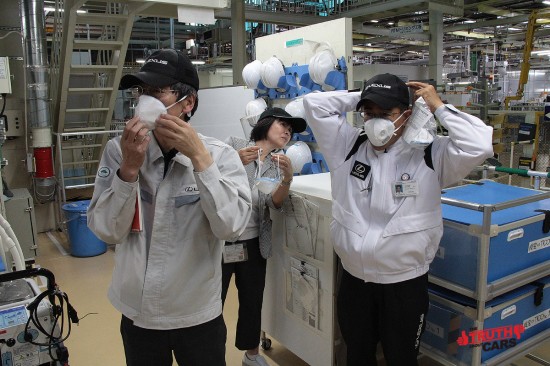
Mặt nạ được trang bị để tránh bụi carbon.
Cỗ máy này được gọi là máy tết 3 chiều. Các nhân viên của Toyota cho biết, trên thế giới hiện nay chỉ tồn tại hai máy như vậy. Một thứ giống như chiếc bít tất đen và dài chạy tới lui 6 lần, trong khi sợi carbon được kéo ra từ 144 cuộn ở xung quanh, đó là quá trình tết carbon lên một khuôn sáp. Lớp chồng lên lớp và đan chéo vào nhau cho đến khi khuôn sáp được phủ kín 12 lớp.
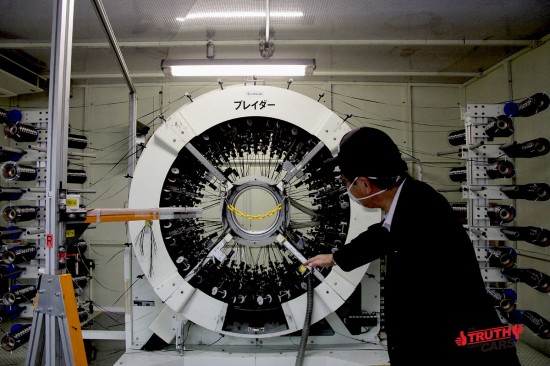
Máy tết 3D gợi nhớ đến chiếc máy dệt cách đây hơn 100 năm của Toyota.
Tết xong, chi tiết được đưa vào máy dập định hình bởi hai mặt khuôn, nhựa nền được bơm vào, gia nhiệt và nén bằng áp suất. Tám giờ sau đó, khuôn sáp tan chảy. Lúc này, kỹ sư trưởng Tanahashi có thể cầm và kiểm tra chi tiết liền khối được tạo thành bởi 12 lớp carbon. Mang mã số T3-3RH, đây sẽ là cột A của chiếc Lexus LFA, một trong những loại cột A mảnh, nhẹ và bền nhất trong ngành công nghiệp ô tô.
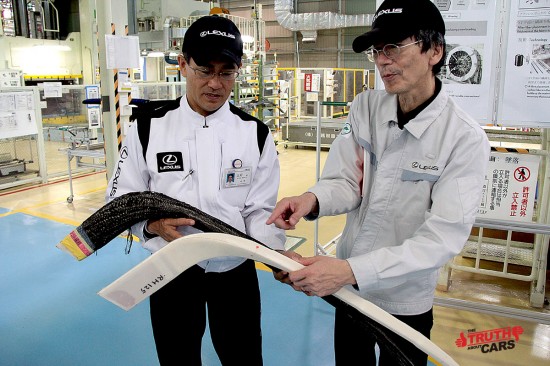
Màu trắng là khuôn sáp ban đầu có dạng như chiếc bít tất, chuyển thành đen sau khi được tết 12 lớp carbon.
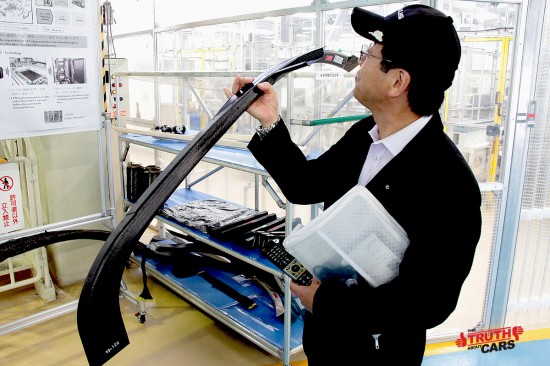
Tanahashi kiểm tra một trong những loại cột A mảnh và cứng nhất trong ngành công nghiệp ô tô.
Chống va đập và các thử nghiệm
Bước qua cánh cửa tiếp theo lại là một chiếc máy kỳ lạ nữa. Thông thường, kỹ thuật dệt chỉ thực hiện theo 2 chiều, cỗ máy này lại có thể dệt theo thức 3 chiều.
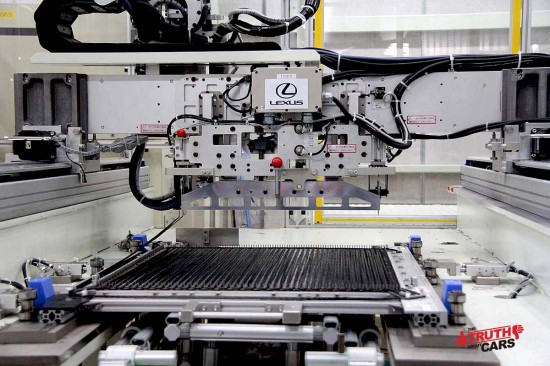
Máy dệt 3D.
Nó đan kết 32 lớp sợi carbon chồng lên nhau với các góc lệch nhau, thành một tấm mỏng. Các tấm carbon này đã được gia cố bằng cách khâu chúng lại với nhau như khâu các lớp chăn. Tuy nhiên, cách thức này có thể gây yếu tấm “chăn” dọc theo các đường chỉ vì lỗ đục của kim khâu. Cỗ máy dệt này tránh được điều đó bằng cách dệt theo cả 3 chiều. Bổ sung thêm nhựa nền, tấm chăn carbon này biến đổi thành chi tiết chống va đập của LFA.
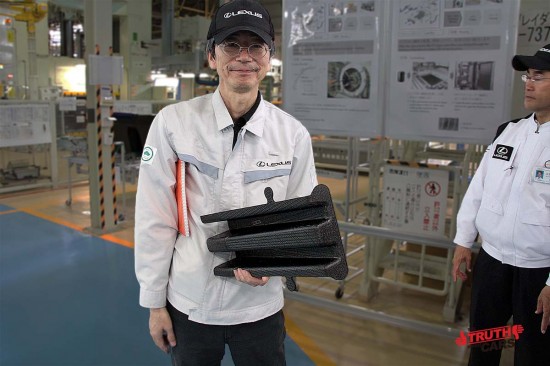
Chi tiết chống va đập.
“Đây là chi tiết để lắp cản trước”, ông Chihura Tamura, Phó giám đốc kỹ thuật dự án LFA nói, và hy vọng chi tiết này sẽ không bao giờ phải chứng minh đặc tính thật sự của nó, vì nó đóng vai trò là hộp chống va đập. Các lớp carbon theo phương thẳng đứng đem lại cho chi tiết này khả năng hấp thụ năng lượng va chạm vượt trội, và là một trong những chi tiết quan trọng nhất trong toàn bộ kết cấu hấp thụ năng lượng va chạm trên ô tô.
Được lắp ở phía trước khung xe, chi tiết này có nhiệm vụ “đợi” các vụ tai nạn xảy ra. Nếu có va chạm, hộp chống va đập hấp thụ và phân tán bớt động năng trước khi các bộ phận của máy móc và người ngồi trong xe bị tác động.
Các loại hộp chống va đập thông thường có thể bẹp dúm trong một vụ va chạm, giống một lon soda bị bóp nát bởi bàn tay chắc khỏe. Hộp chống va đập của LFA không dẹp dúm mà thay vào đó là bị vụn ra. Hình ảnh ghi lại bởi camera siêu tốc trong một cuộc thử nghiệm va chạm cho thấy cách thức mà loại vật liệu này bị phá hủy. Hộp chống va đập vỡ vụn ra thành hàng triệu mảnh nhỏ, và mỗi mảnh cần phải có một năng lượng nhất định để bị tách rời ra khỏi khối. Đó là cách mà chi tiết này giảm thiểu năng lượng va đập và hạn chế thiệt hại cũng như thương tổn.
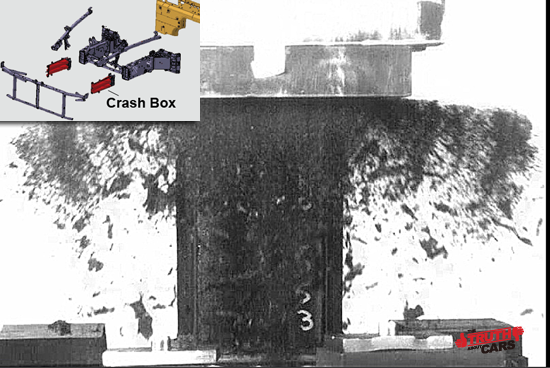
Hình ảnh được camera siêu tốc ghi lại trong một cuộc thử nghiệm va đập cho thấy cách thức mà carbon trên bộ phận chống va đập của LFA bị phá hủy.
Ngày nay, vô số các cuộc va chạm được mô phỏng trên máy tính, và sau đó, để chắc ăn, người ta còn thực hiện hàng loạt vụ va chạm trên thực tế. Mô phỏng cách thức biến dạng của kim loại là khá đơn giản. Tuy nhiên, với CFRP, các kỹ sư phải vùi đầu vào một loạt các tham số, bao chất lượng của sợi carbon, định hướng sợi, mật độ sợi, vật liệu nhựa nền được sử dụng, số lớp, góc xếp của từng lớp, phương pháp chế tạo và nhiều yếu tố khác. Trong quá trình nghiên cứu, đầu tiên, đội ngũ LFA chế tạo một mẫu vật liệu nhỏ, thử nghiệm chúng, sau đó sử dụng các đặc tính thu được cho những lần thử nghiệm lớn hơn. “Số lượng các vụ thử nghiệm va chạm với LFA lớn hơn rất nhiều so với các mẫu xe thông thường khác”, Tamura cho biết.
Phương pháp chế tạo khác nhau
Cột A chống đỡ mui ra đời từ máy tết, nhưng hộp chống va đập và nhiều chi tiết CFRP khác của LFA lại được sản xuất bởi một phương pháp khác, có tên là Resin Transfer Molding (RTM) – đổ nhựa nền lên khuôn. Với phương pháp RTM, sợi carbon khô được xếp trên một chiếc khuôn, nhựa nền dạng lỏng sẽ được quết lên lớp sợi carbon khô này. Dưới áp suất 3 bar và nhiệt độ 130 độ C, chi tiết được làm khô, sau đó đem gia công hoàn thiện với máy cắt bằng tia nước áp suất cao.
RTM là phương pháp dễ tiến gần đến khả năng sản xuất đại trà nhất, tuy nhiên vẫn còn một chặng đường dài phía trước. Phương pháp này tiết kiệm được công đoạn xếp lớp Pre-preg nặng nhọc, đồng thời không cần tới nồi hấp khổng lồ. Tuy nhiên, các chi tiết gia công vẫn cần phải được giữ trên khuôn khoảng 8 tiếng để nhựa nền đông cứng, nghĩa là chỉ tiết kiệm được một nửa thời gian gia công.
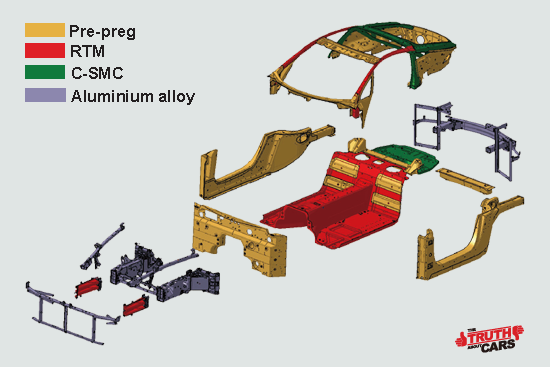
Sơ đồ phân bố các chi tiết CFRP được sản xuất theo các phương pháp khác nhau, tùy thuộc vào yêu cầu chịu lực của chúng.
Phương pháp xử lý thứ 3 được gọi là Sheet Molding Compound (SMC). Trong phương pháp này, các mẫu carbon nhỏ dài khoảng 1 inch được trộn với nhựa nền. Hỗn hợp này sau đó được đổ vào khuôn, gia nhiệt và gia áp. Đây là loại CFRP “bình dân” nhất sử dụng trên LFA. Loại này sử dụng cho một số chi tiết đòi hỏi độ bền chịu lực kém như các panel bên hông, chắn bùn, thêm một vài chi tiết phía sau xe, đồng thời là dạng CFRP duy nhất được thực hiện bởi các đối tác bên ngoài nhà máy.
Thông thường, hầu hết các công việc nặng nhọc trong quá trình sản xuất ô tô được thực hiện bởi cánh tay robot. Tuy nhiên, tại phân xưởng LFA, robot chỉ có nhiệm vụ như một thiết bị gắn kết các chi tiết CFRP đơn giản. Được nối với 1 chiếc ống dài, cánh tay robot này lần lượt bơm nhựa nền để liên kết các chi tiết rời thành một khối thống nhất, đây là những bộ phận carbon xung quanh 2 ghế ngồi trên xe, nhẹ nhưng vẫn đảm bảo độ cứng và bền.
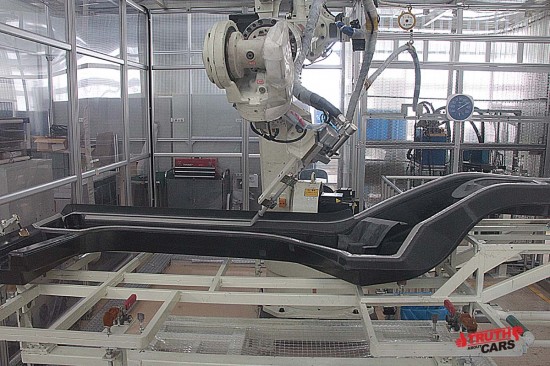
Cánh tay robot tiến hành ghép nối các chi tiết bằng keo nhựa.
Tổng thời gian để dựng lên một bộ khung cho LFA mất 4 ngày. Cuối ngày thứ tư, thành quả là một bộ khung hoàn thiện thô (chưa sơn) mà trong ngành công nghiệp ô tô vẫn quen được gọi là body-in-white (khung trắng). Tuy nhiên, trong trường hợp của LFA, người ta gọi nó là body-in-black, bởi phần lớn khung của mẫu xe này được chế tạo từ carbon.
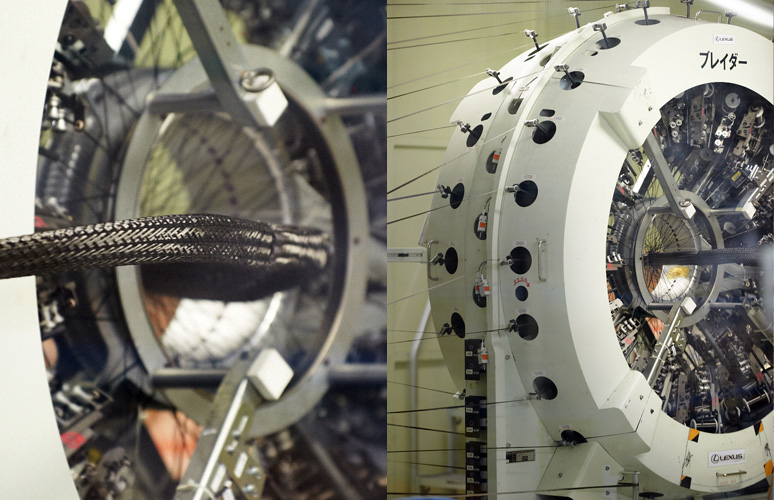
Mỗi chiếc Lexus LFA được cấu thành bởi khoảng 10.000 chi tiết, bao gồm tất cả các hệ thống, từ động cơ, hệ truyền lực, khung xe và tất cả các chi tiết khác làm từ sợi carbon. Các chi tiết này xuất phát điểm chỉ là những sợi carbon, thông qua máy tết 3D và máy dệt, chúng trở thành những chi tiết nhiều hình dạng, nhẹ, bền và cứng nhất trong ngành sản xuất ô tô.
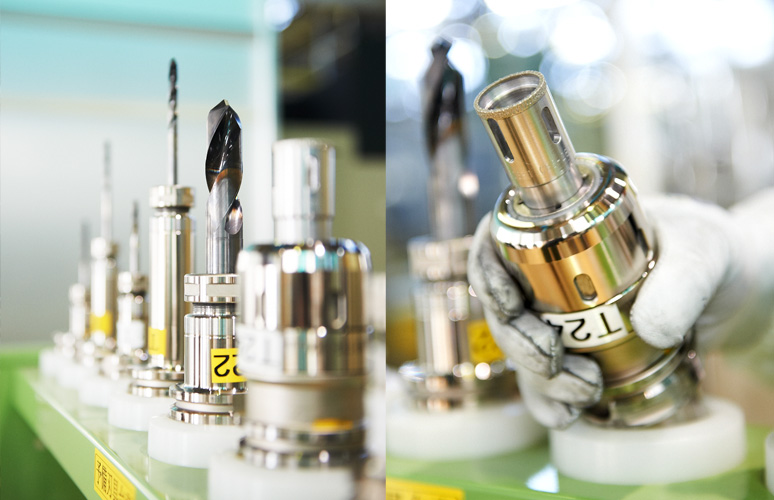
Khi định hình xong, khung xe được khoan nhiều lỗ để luồn cáp điện và các loại ống dẫn. Vì đặc tính cứng và bên, quá trình khoan này không phải là một công việc dễ dàng. “Carbon có tính chất độc đáo và phức tạp, giống như gỗ tre dưới mũi khoan. Mỗi ngày tôi lại phát hiện ra một điều gì đó mới về nó. Để hoàn thành công đoạn này, chúng tôi phải thực hiện 32 mũi khoan với các đầu khoan kim cương nhằm đạt được vết khoan tinh xảo nhất”, chuyên gia khoan Akira Yamaguchi giải thích.
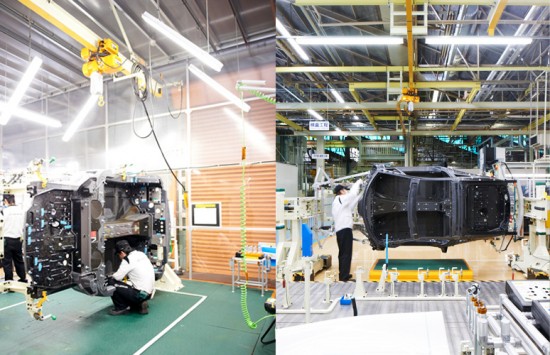
Khi bộ khung hoàn thiện, các bề mặt còn thô ráp được xử lý bằng phương pháp mài và rửa để chuẩn bị cho các bước ghép nối tiếp theo. Trước khi ghép nối, bộ khung này không chỉ được kiểm tra hình dạng và biến dạng bằng tay mà còn được dò bằng máy với 567 điểm dò.
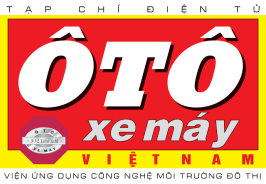