Nanoslide - Bí mật động cơ Diesel của Mercedes
Động cơ Diesel chính thức ra đời từ năm 1892 bởi nhà phát minh, kỹ sư chế tạo máy Rudolf Christian Karl Diesel. Cho đến nay, nhờ công nghệ vật liệu và sự phát triển mạnh mẽ của nền cơ khí hiện đại, nhược điểm của động cơ diesel truyền thống đã được khắc phục. Sự hiện diện của động cơ diesel trên những chiếc xe hơi ngày càng phổ biến. Trong cuộc phát kiến phát triển động cơ diesel, Mercedes là người tiên phong và dường như là kẻ đầu tiên về đích.
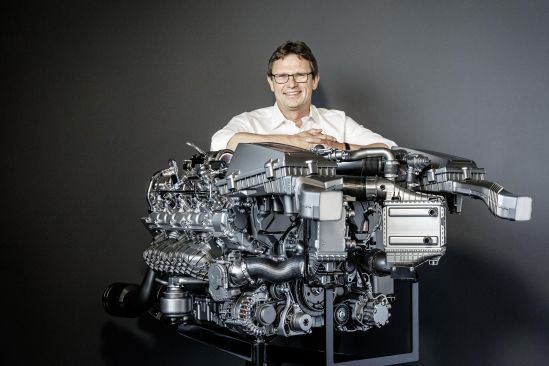
Năm 1936, Mercedes là nhà sản xuất đầu tiên trên thế giới ứng dụng động cơ diesel vào nền công nghiệp ôtô dân dụng - chiếc 260D trở thành chiếc xe hơi đầu tiên trên thế giới sử dụng động cơ diesel. Tiếp tục con đường tự mình phát kiến, Mercedes phát triển và tập trung vào việc giảm thiểu những nhược điểm của động cơ diesel chủ yếu bằng những thành tựu về công nghệ vật liệu để cạnh tranh với đối thủ không đội trời chung BMW, Audi và những “kẻ lạc dòng” đến từ châu Á như: Toyota, Huyndai... hay “gã cơ bắp” Ford đến từ Châu Mỹ.
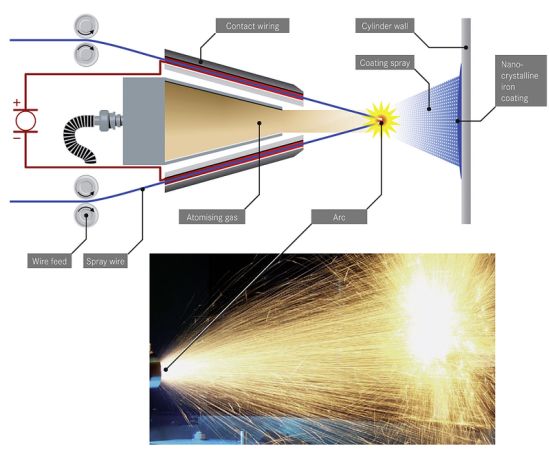
Mercedes phải nỗ lực cạnh tranh ngay trên con đường mình phát kiến.
Sau gần 7 thập kỉ nghiên cứu và phát triển, Mercedes đã cho ra đời động cơ BlueTEC, đáp ứng những yêu cầu khắt khe về khí thải cùng những con số trong bài toán kinh tế ấn tượng đối với một động cơ diesel. Những kỹ sư trong phòng nghiên cứu của tập đoàn Daimler AG đã làm việc không ngừng nghỉ để phát triển dòng động cơ mới. Bí mật gì đang gợi mở ra một tương lai tươi sáng cho động cơ diesel trong tương lai? Tất cả nằm trong phòng công nghệ vật liệu tiên tiến trong trung tâm nghiên cứu công nghệ động cơ xanh Mercedes-Benz Werk Mannheim.
Công nghệ phun phủ bề mặt NANOSLIDE
Công nghệ phun phủ bề mặt đã được ứng dụng rất nhiều trong các ngành công nghiệp vật liệu nhằm tạo ra bề mặt làm việc đáp ứng cơ tính và tính chất làm việc rất cao trên nền vật liệu cơ bản. Nhờ năng lượng hồ quang hoặc năng lượng tia plasma (với phương pháp phun phủ plasma- bột), kim loại nền nóng chảy và được phủ bởi lớp vật liệu bề mặt cung cấp từ dây bù (hoặc bột phủ) mang cơ-lý tính yêu cầu.
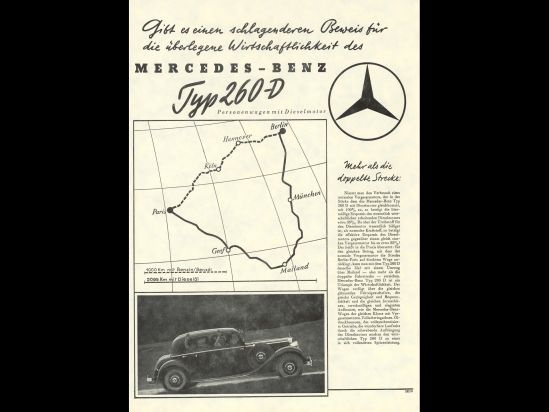
Nhờ ứng dụng công nghệ NANOSLIDE, sau 5 năm sử dụng động cơ độc quyền của AMG, giờ đây Mercedes có thể chế tạo xi-lanh bằng hợp kim nhôm và ứng dụng công nghệ phun phủ để tạo bề mặt làm việc cho xi-lanh có cơ-lý tính ưu việt hơn so với xi-lanh bằng gang - vật liệu truyền thống. Nhờ đó, khối lượng động cơ giảm đáng kể đồng thời hiệu quả tản nhiệt của động cơ được nâng cao. Cơ- lý tính của bề mặt làm việc của xi-lanh đáp ứng được những yêu cầu rất cao của chế độ làm việc trên chiều dày chỉ từ 0.1-0.15mm. Bề mặt làm việc siêu bóng và siêu bền của xi-lanh chế tạo bằng phương pháp mới không những giúp giảm ma sát, thay đổi dung sai lắp ráp giữa piston và xi-lanh theo hướng có lợi ( hiệu quả hơn 50% so với xi-lanh gang đúc truyền thống), các kỹ sư của Mercedes còn phát hiện bề mặt xi-lanh còn có tính chất xốp ( nhờ phương pháp gia công phun phủ chứ không dùng các phương pháp đúc, cắt gọt truyền thống), nhờ vậy tăng khả năng lưu dầu, giúp tăng khả năng bôi trơn và kéo dài tuổi thọ.
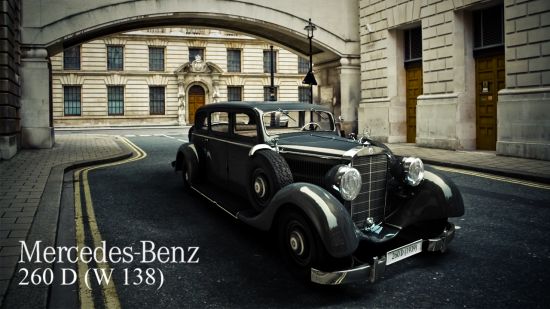
Mercedes chứng tỏ là một nhà sản xuất có rất nhiều kinh nghiệm sử dụng vật liệu tiên tiến trong các sản phẩm của mình. Tháng 7 năm 2005, Mercedes- AMG GmbH giới thiệu động cơ V8 6.3 với những số liệu về hiệu suất vượt trội. Tiếp tục thành công đó, Mercedes sản xuất thương mại dòng động cơ mới ứng dụng công nghệ phun phủ bề mặt xi-lanh trên nền hợp kim nhôm. Tới năm 2006, công nghệ tiên tiến này đã trở thành thành phần quan trọng trong thành công của dòng động cơ 6.3 của AMG. Đến nay, hơn 75.000 động cơ AMG ứng dụng công nghệ này đã đáp ứng kỳ vọng của Mercedes, đem đến sự hài lòng từ khách hàng, đánh giá cao của các chuyên gia và là nỗi lo lắng của những đối thủ trong nền công nghiệp oto vốn đầy cạnh tranh. Mercedes chăm chút cho “con gà đẻ quả trứng vàng” bằng hơn 90 bằng sáng chế chia sẻ và hơn 40 bằng sáng chế, để đảm bảo vị trí độc quyền của mình trong công nghệ này.
Khi mà các phân khúc xe hơi ngày càng trở nên đa dạng và sự cạnh tranh khốc liệt giữa các hãng xe, Mercedes đưa con bài tủ của mình vào dòng động cơ V6 Diesel, đánh dấu cho sự phát triển mới cực kì mạnh mẽ trên cuộc chiến động cơ Diesel thế hệ mới. Kết quả, thế hệ động cơ V6 Diesel mới nhẹ hơn 4.3 kg, tiết kiệm nhiên liệu hơn 3% so với dòng động cơ cũ. Chiếc ML 350 BlueTEC có sức mạnh 258 mã lực ( 190kW) từ khối động cơ dung tích 2987cc, mô-men xoắn 620 Nm. Với mức tiêu thụ lý thuyết 6.8 lít cho 100km, động cơ mới tiết kiệm 2.1 lít ( tương đương 24%) so với thế hệ cũ. Lượng khí thải CO2 từ 235-179g/km. Nhờ kết hợp công nghệ BlueTEC và công nghệ xử lý khí thải AdBlue®, dòng M-class của Mercedes đạt tiêu chuẩn khí thải Euro-6 và là một trong những động cơ diesel sạch nhất thế giới.
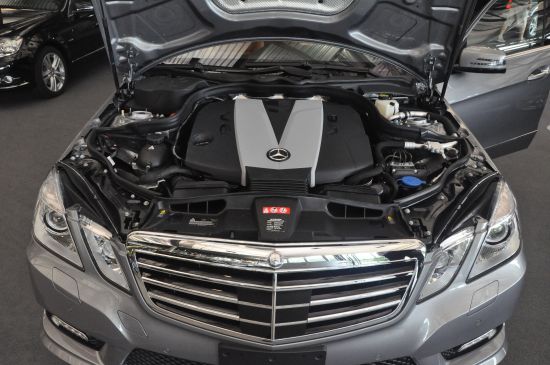
Bước tiến mới của công nghệ chế tạo piston
Đầu tháng 9-2014, Mercedes tiếp tục giới thiệu thành công trong việc ứng dụng piston thép hợp kim công nghệ cao thay thế cho piston hợp kim nhôm truyền thống. Đây là một bước thành công góp phần hoàn thiện công nghệ động cơ diesel mà Mercedes đã theo đuổi gần 70 năm qua. Động cơ V6 350 BlueTEC thế hệ mới sử dụng piston thép hợp kim công nghệ cao sẽ có mặt đầu tiên trên các dòng E-class của Mercedes.
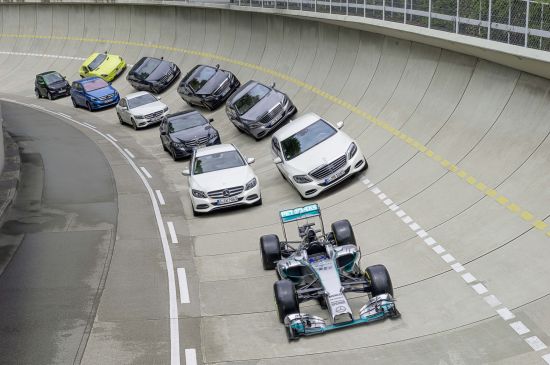
Trước đó, đã có nhiều ý tưởng sử dụng kết hợp hai loại vật liệu thép – nhôm. Khó khăn là độ dãn nở của thép lớn hơn, tản nhiệt kém và khối lượng riêng cao hơn của nhôm. Các kỹ sư của Mercedes đã nghiên cứu và kết hợp hài hòa, hoàn hảo trên những động cơ sử dụng xi-lanh mới ứng dụng công nghệ NANOSLIDE.
Theo kết quả thử nghiệm, piston mới cho công suất đầu ra tương đương với động cơ sử dụng piston nhôm truyền thống (190kW/ 258hp), tuy nhiên mức tiêu thụ nhiên liệu có thể giảm xuống còn 5.0 lít/100km- giảm khoảng 3% so với piston hợp kim nhôm. Sở dĩ có sự khác biệt đó là nhờ sử dụng vật liệu thép hợp kim cao có cơ tính vượt trội hơn hẳn so với hợp kim nhôm truyền thống, cùng một yêu cầu cơ-lý tính tương đương, piston mới có kích thước và khối lượng nhỏ hơn piston nhôm.
Nhờ việc giảm dung sai khi lắp ráp piston – xi-lanh xuống từ 40-50% so với dung sai lắp ráp piston nhôm truyền thống, ở dải nhiệt độ thấp piston và xi-lanh tạo buồng đốt kín hơn so với buồng đốt sử dụng piston – xi-lanh truyền thống, do đó tăng hiệu quả đốt cháy và giảm nồng độ khí thải. Khi động cơ làm việc ở tua máy cao khiến nhiệt độ tăng, do nhôm dãn nở nhiệt cao hơn thép, khe hở giữa piston và xi-lanh tăng làm giảm ma sát, qua đó giảm công hao phí, giúp tiết kiệm nhiên liệu. Song song đó, tính dẫn nhiệt của hợp kim thép công nghệ cao chế tạo piston kém hơn hợp kim nhôm trên piston truyền thống nên nhiệt ở buồng đốt sẽ được lưu giữ ở mức độ có lợi cho các quá trình nhiệt động lực học. Vấn đề tản nhiệt giải quyết dễ dàng nhờ thân xi-lanh được chế tạo bằng hợp kim nhôm- vật liệu có tính dẫn nhiệt tốt.
Trải qua gần 70 năm phát triển, kể từ khi chiếc Mercedes-Benz 260D chạy máy “dầu” đầu tiên được giới thiệu, những công nghệ động cơ được Mercedes chọn lọc và ứng dụng phát triển liên tục. Như công nghệ turbo trong những năm 70, công nghệ lọc khí thải được Mercedes ứng dụng năm 1985, động cơ điều khiển điện tử “common-rail” ứng dụng năm 1997…vv. Giờ đây với thành công trong việc sử dụng vật liệu mới sẽ lại tiếp tục giữ vững danh hiệu vô địch “máy dầu” cho động cơ của Mercedes-Benz.
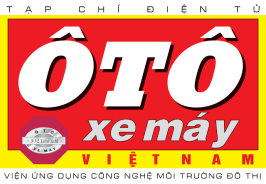